The directive emphasizes the need to develop the building materials industry efficiently and sustainably, ensuring it meets domestic demand while increasing exports of high-value products.
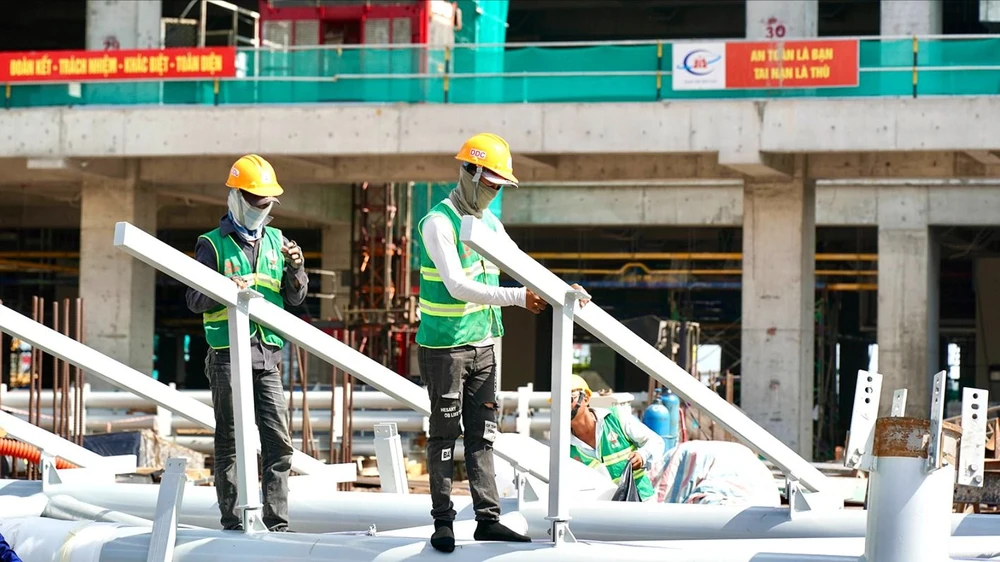
Sharp decline in production and sales
According to the Ministry of Construction, production and sales of building materials have continued to drop heavily throughout 2023 and the first eight months of 2024. In the cement industry, total production for 2023 was only 92.9 million tons out of a capacity of 122.34 million tons per year. This shortfall led to 42 out of 92 production lines being halted for one to six months, with some lines ceasing operations for the entire year. This trend has extended into 2024, with cement plants operating at only 70-75 percent of their designed capacity. Additionally, cement inventory has now exceeded 5 million tons.
The current production capacity of the construction glass sector is 5,900 tons per day, equivalent to 331 million square meters per year. However, since 2023, three production lines have been idle for over six months, one project has been suspended, and glass consumption has slumped by 33 percent compared to 2020. Similarly, the ceramics and tile sectors have experienced a 35-40 percent decrease in consumption.
According to Mr. Nguyen Van Sinh, Deputy Minister of Construction, the domestic building materials industry has been impacted by the downturn in the real estate market, reduced construction investment, and delays in infrastructure and housing projects. Additionally, increased transportation costs have driven up building material prices, while the growing influx of imported materials has further affected the market.
Mr. Tong Van Nga, Chairman of Vietnam Building Materials Association, reported that the annual revenue of the building materials sector (excluding construction steel) is estimated at around VND600 trillion (over US$24 billion), accounting for nearly 6 percent of the national GDP. This sector significantly contributes to State revenue and provides employment for millions of people.
However, in recent years, the industry has faced numerous difficulties, leading to stagnation in production and business activities and negatively impacting the country’s socio-economic development. Many companies are now burdened with substantial debt. Rising bank interest rates have created challenges in managing capital and increasing the risk of bad debt for building material manufacturers, particularly cement manufacturers.
Synchronizing a range of solutions
The Ministry of Construction has noted that domestic demand for building materials remains high, due to low national housing coverage, an urbanization rate of only about 43 percent, and incomplete infrastructure systems for transportation and energy. The national urbanization goal is set at 70-75 percent by 2050, requiring an annual increase in the construction area of at least 20 million square meters.
For instance, to achieve the target of building 1 million social housing units from 2021 to 2030, around 150,000 units need to be constructed each year. This would necessitate 4 million tons of cement and 1 million tons of steel and would drive demand for other materials such as sanitary ceramics, tiles, and construction glass. Additionally, there is demand for building materials for numerous ongoing and future large-scale transportation projects planned up to 2030 and beyond, according to the approved master plan.
Therefore, finding solutions to address the challenges facing the building materials industry has become critically urgent. From the perspective of managing the real estate market and construction activities, the Ministry of Construction recommends that relevant ministries and local authorities focus on boosting public investment and infrastructure development, resolving issues in the real estate and housing markets, and expediting the construction of at least 1 million social housing units. Additionally, there should be increased use of reinforced concrete viaducts in highway projects.
Mr. Tong Van Nga suggests that, in addition to focusing on social housing development, industrial zone plans should include provisions for worker housing, which would positively impact the building materials market. Mr. Le Quang Hung, Chairman of Vietnam Concrete Association, believes that increasing the construction of viaducts on national highways and expressways could help absorb 70-80 percent of the current cement inventory.
Meanwhile, for the building materials industry to achieve sustainable development, Mr. Pham Van Bac, Vice Chairman of Vietnam Building Materials Association, recommends that the government and relevant ministries develop mechanisms and policies to foster an investment environment for new, advanced building materials that are economically valuable, energy-efficient, and environmentally friendly. Furthermore, strategies for building materials development and the planning of mineral resources should be reviewed and adjusted as necessary to align with the country's evolving needs.
Mr. Nguyen Quang Cung, Chairman of Vietnam National Cement Association (VNCA):
The VNCA has recommended that the government direct the construction of elevated and reinforced concrete roads instead of earth embankment roads where appropriate. This technology enhances the quality and durability of infrastructure and has been utilized in Europe and the United States for many years. With the government currently prioritizing resources for sustainable infrastructure projects in the Mekong Delta region, early implementation of these projects would present a significant opportunity for the cement industry in particular and the building materials sector, in general.
Mr. Tong Van Nga, Chairman of Vietnam Building Materials Association:
The use of elevated roads on national highways and expressways remains relatively low, at less than 10 percent. Utilizing cement for constructing roads and elevated structures in areas with weak soil, such as the Mekong Delta, can help conserve scarce embankment materials and improve the infrastructure's ability to withstand climate change because elevated roads provide better water drainage, enhancing the durability of the structures.